Spray Drying Of Dispersible Latex Powder And Urea Formaldehyde Resin
Redispersible polymer powder is a powdery thermoplastic resin made by spray drying and subsequent treatment of high molecular polymer emulsions. It is usually a white powder, but a few contain other colors. Mainly used in construction, especially in increasing cohesion, cohesion, and flexibility of dry-mixed mortar.
The production of redispersible rubber powder is mainly divided into two steps: the first step is to produce a polymer emulsion through emulsion polymerization, and the second step is to spray-dry a mixture prepared from the polymer emulsion to obtain a polymer powder.
Drying process: The prepared polymer emulsion is transported to a spray dryer by a screw pump for drying. The temperature at the inlet of the dryer is generally 100 ~ 200ºC, and the outlet is generally 60 ~ 80 ºC. Because spray drying occurs within a few seconds, the distribution of the particles is "frozen" at this time, and the protective colloid acts as a spacer particle to isolate it, thereby preventing irreversible coalescence of the polymer particles. In order to prevent the redispersible rubber powder from "caking" during transportation and storage, an anti-caking agent needs to be added during or after spray drying.
1. Material: polymer emulsion
2. Dry powder output: 100 kg /h ~ 700kg /h
3. Solid content: 30% ~ 42%
4. Heat source: natural gas burner, diesel burner, superheated steam, biological particle burner, etc. (It can be replaced according to customer conditions)
5. Atomization method: high-speed centrifugal atomizer
6. Material recovery: Two-stage bag dust removal is adopted, with a recovery rate of 99.8%, which meets national emission standards.
7. Material collection: Material Collection: Adopt Centralized Material Collection. From the bottom of the tower to the bag filter, the powder is sent to the receiving small bag by the air conveying system, and then screened remaining material to the silo by vibrating screen, and finally to the automatic packing machine after iron removal.
8. Auxiliary material adding method: Two automatic feeding machines add quantitative at the top of two points. The feeding machine is equipped with a weighing system, which can accurately feed any amount.
9, electrical control: PLC program control. (Inlet air temperature automatic control, outlet air temperature automatic control, atomizer oil temperature, oil pressure alarm, negative pressure display in the tower) or full computer DCS control.
Urea-formaldehyde resin adhesive, with high gluing strength, good temperature, water and corrosion resistance. In addition, because the resin itself is transparent or milky white, the color of made-up particleboard and MDF is beautiful, finished plywood without contamination, used in wood products does not affect the appearance. Urea-formaldehyde resin glue powder is made of liquid resin spray drying, is a single-component powder adhesive, it has many excellent properties, such as water resistance, mildew resistance, yellowing resistance, strong adhesion, aging resistance, cold pressing or hot pressing, easy deformation, convenient operation and long storage life. It is suitable for the bonding of curved wood, veneer, edge, particleboard and MDF. It is an ideal adhesive for furniture assembly and wood bonding.
The prepared resin emulsion is conveyed to the high-speed centrifugal atomizer by screw pump, which is atomized into a large number of small droplets of uniform size, in contact with the hot air in the drying tower, water is quickly evaporated out, water vapor and dry powder then enter the cloth bag duster, water vapor through the filter bag into the induced draft fan discharge to the air. The dry powder is lowered to the bottom of the bag filter due to the pressure drop, through the rotary valve and air conveying pipe to the centralized receiving small cloth bag, and then vibrating sieve screen to the silo, and finally remove iron to the automatic packaging machine after receiving material. In order to prevent "caking" during conveying and storage of the redispersible powders, an anti-caking agent is added during spray drying using a screw feeder.
1. Material: urea-formaldehyde resin emulsion
2. Dry powder output: 100 kg / h ~ 1000kg / h
3. Solid content: 45% ~ 55%
4. Heat source: natural gas burner, diesel burner, superheated steam, biological particle burner, etc. (It can be replaced according to customer conditions)
5. Atomization method: high-speed centrifugal atomizer
6. Material recovery: Two-stage bag dust removal is adopted, with a recovery rate of 99.8%, which meets national emission standards.
7. Material collection: Material Collection: Adopt Centralized Material Collection. From the bottom of the tower to the bag filter, the powder is sent to the receiving small bag by the air conveying system, and then screened remaining material to the silo by vibrating screen, and finally to the automatic packing machine after iron removal.
8. Auxiliary material adding method: Two automatic feeding machines add quantitative at the top of two points. The feeding machine is equipped with a weighing system, which can accurately feed any amount.
9, electrical control: PLC program control. (Inlet air temperature automatic control, outlet air temperature automatic control, atomizer oil temperature, oil pressure alarm, negative pressure display in the tower) or full computer DCS control.
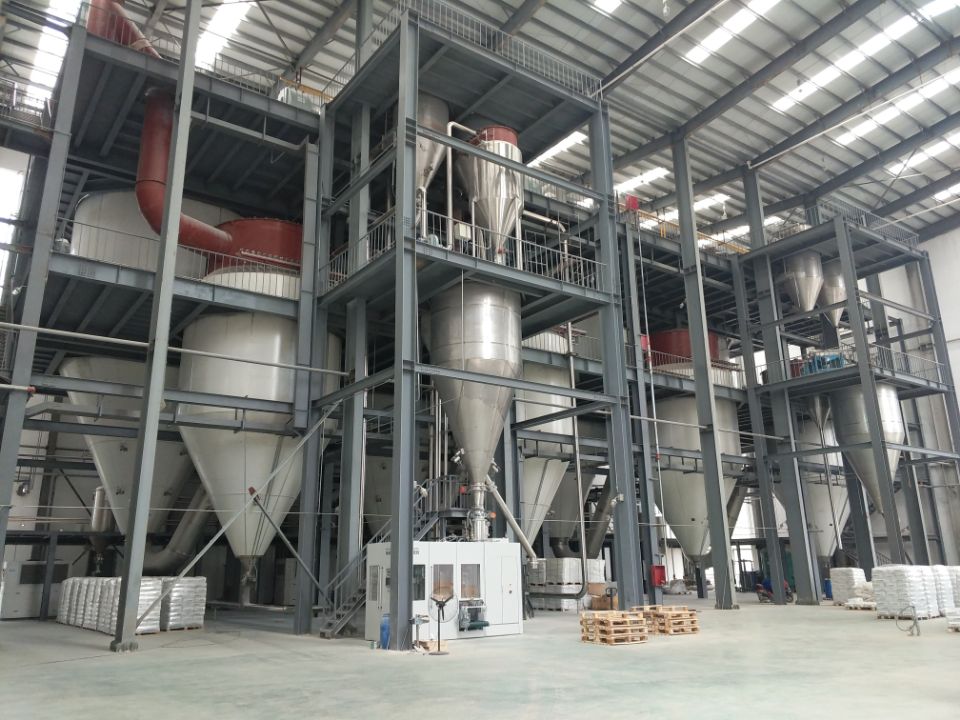
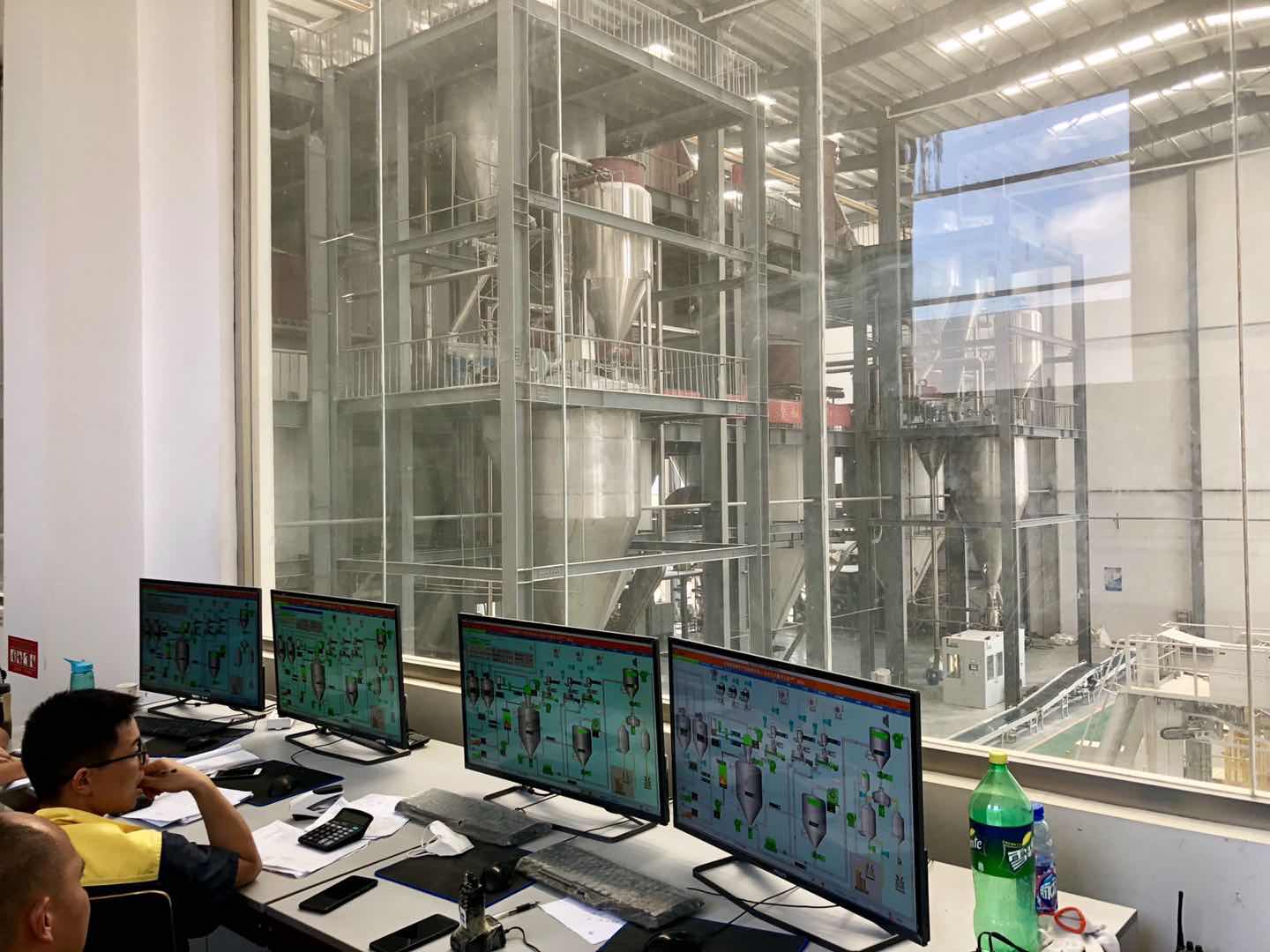

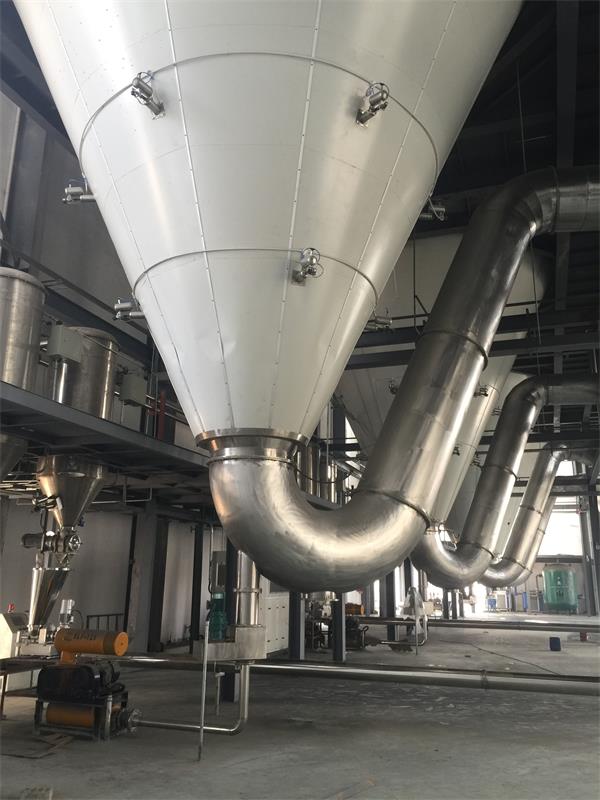
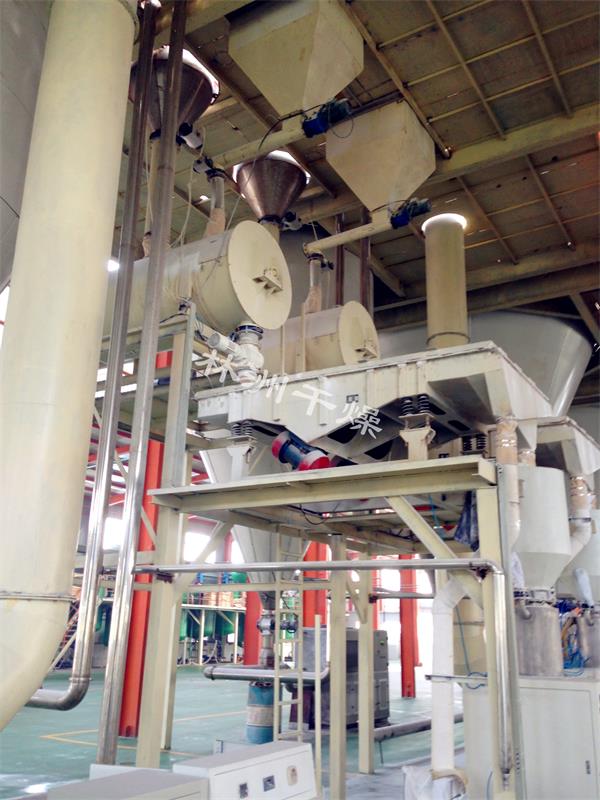