Resource Treatment of Bio-fermentation Wastewater by Spray Drying
Clean production, zero discharge of industrial wastewater, and achieving a beautiful ecological environment have always been people's pursuit of goals, but in actual industrial production, it is not easy to achieve, especially high concentration wastewater, which needs to be diluted, filtered, neutralized and oxidized and biochemical treatment methods, in order to treat wastewater into qualified second and third class of water. Traditional wastewater treatment methods have increased the operating costs of enterprises, making it impossible for companies to guarantee the conscious treatment of industrial wastewater; however, the spray drying equipment produced by our company can solve this problem.
Wastewater is also a resource.Biochemical industry, inorganic salt chemical industry, food industry, meat processing, paper industry, alcohol and other industrial wastewater containing cellulose, sugar, protein, nitrogen-based acid, inorganic salt and other useful resources, throw away is harmful, take out is treasure, the treatment of waste water to extract useful resources, waste water through evaporation into steam condensed water, is not waste water,To achieve clean production and a truly beautiful environment.
Some useful substances such as protein in the wastewater can be converted into steam condensate by one or more stages of separation and spray drying, and the useful substances in the wastewater can be turned into feed additives, such as meat The blood water and meat washing water in the combined processing plant were thrown away as waste water in the past, which polluted the environment and lost resources. Foreign countries have used this process to recover all blood proteins and sell them to feed plants. The combined plant has achieved economic benefits, killing two birds with one stone. In the starch industry, corn, wheat, potatoes, etc., washing water and soaking water contain starch, protein, lactic acid, and the like. Many domestic starch factories have discarded it as waste water, which can be evaporated and concentrated to 50%, and then spray-dried into protein feed additives, while soaking water becomes steam condensate, which can be recycled as process water. The rotten environment of the starch factory is gone forever, and at the same time it produces economic benefits.
The above-mentioned technologies are all physical processes without chemical reactions and are technically mature and reliable. When Chinese people master these technologies, there are new developments and innovations, but to complete an engineering design, the balance of materials and heat must be calculated. This requires the cooperation of enterprises to provide the basic physical and chemical parameters of the Wstewater.
Classification Of Wastewater From Bio-Fermentation Liquor & Application Of Spray Drying Production
Monosodium glutamate wastewater | |
Disjunctive Tail Concentrated Liquid | Compound fertilizer |
Corn pulp | Protein feed additive |
Biopharmaceutical waste water | |
Vitamin B2 waste water | Feed additive |
Cephalosporin waste water | Feed Additives |
Yeast waste wate | Protein feed additives, at the same time, can be further processed into yeast protein peptide |
Alcohol waste water | Organic Compound Fertilizer |
Heparin sodium waste water | Protein feed additives, which can be further |
Chondroitin waste water | Protein feed additives, which can be further |
1. Material: suitable for various materials
2. Air inlet temperature: 120 ℃ ~ 700 ℃
3. Air outlet temperature: 60 ℃ ~ 400 ℃
4. Dry powder output: 50 kg / H ~ 4000kg / h
5. Solid content: 5% ~ 55%
6. Heat source: electric heating, steam power on, natural gas combustion furnace, diesel combustion furnace, superheated steam, bio particle combustion furnace, coal-fired furnace, etc. (can be replaced according to customer conditions)
7. Atomization mode: high speed centrifugal atomizer, pressure spray gun
8. Material recovery:
a. Primary cyclone dust removal (recovery 97%)
b. Primary cyclone dedusting, water film dedusting (recovery 97%, 0 discharge)
c. Primary cyclone dedusting plus bag dedusting (recovery 99.8%, 0 discharge)
d. Two stage bag dedusting (recovery 99.9%, 0 discharge)
9. Electrical control: (air inlet temperature automatic control, air outlet temperature automatic control, atomizer oil temperature, oil pressure alarm, negative pressure display in the tower)
a. PLC program control
b. Full computer DCS control
c. Electric cabinet button control
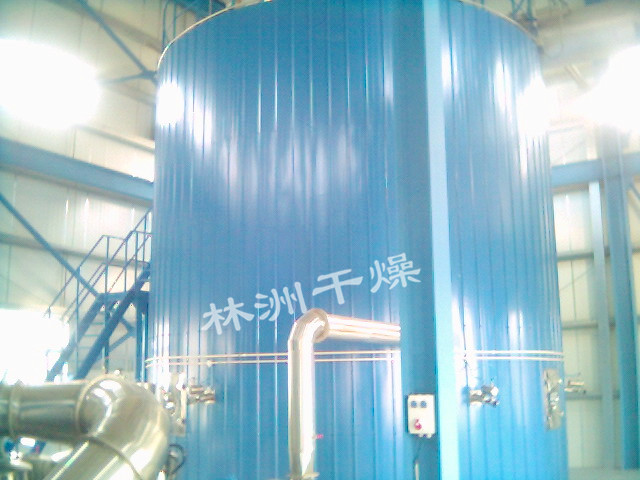
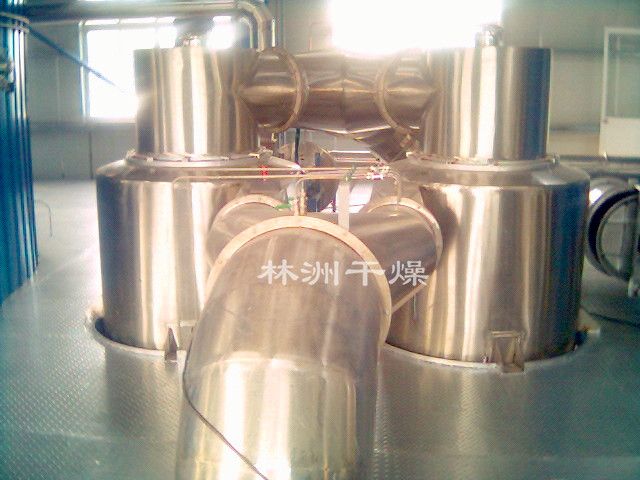
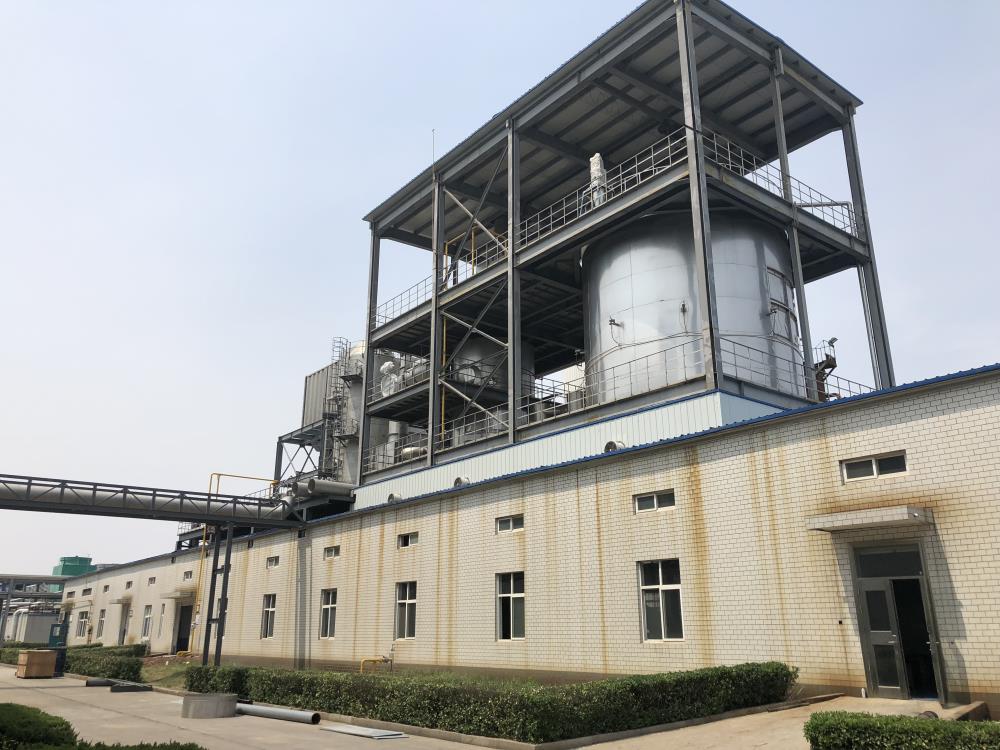
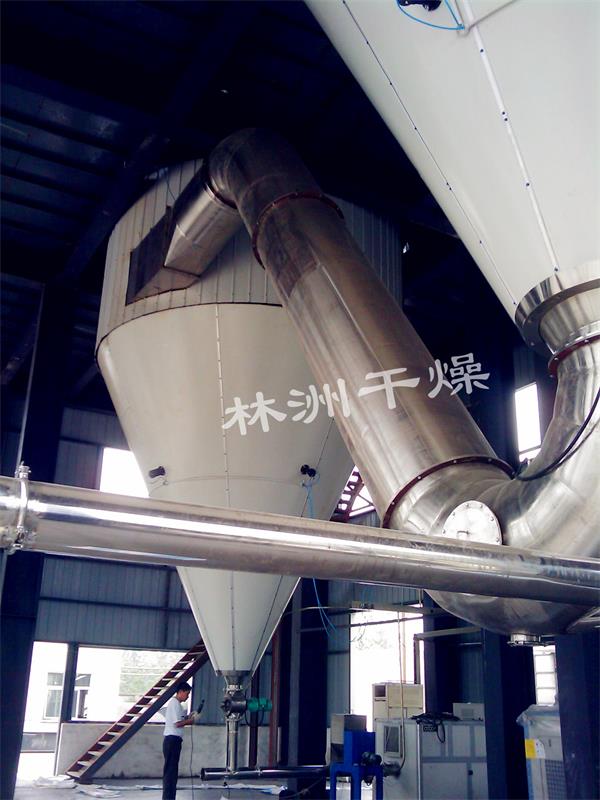