Ceramics
Alumina ceramic is a kind of wear-resistant, corrosion-resistant and high-strength ceramic material.It is widely used and is currently the most widely used category of high-temperature structural ceramics. In order to form mass production and meet the requirements of regular product appearance, small grinding amount and easy fine grinding, it is very necessary to choose the forming method of dry pressing.Compression molding requires that the blank is a powder with a certain gradation, with less moisture and binder.Therefore, the slurry of the batch after ball milling and fine crushing must be dried and granulated to obtain the powder with better fluidity and higher bulk density. Spray drying granulation has become the basic method for the production of building ceramics and new ceramics.The powder prepared by this process has good fluidity, a certain proportion of large and small particles, and good bulk density.Therefore, spray drying is the most effective method to prepare dry pressed powder.
Spray drying is a process in which liquid materials (including slurry) are atomized and then converted into dry powder materials in a hot drying medium. The materials are atomized into extremely fine spherical fogdrops, due to the fogdrops are very fine and the ratio of surface area to volume is very large, the moisture rapidly evaporates, and the drying and granulation processes are completed in an instant. The particle size, moisture content and bulk density of the materials can be controlled by adjusting drying operation parameters. Spherical powder with uniform quality and good repeatability can be produced by adopting spray drying technology, thus shortening the production process of powder, facilitating automatic and continuous production, and being an effective method for large-scale preparation of fine alumina ceramic dry powder materials.
2.1.1 Preparation of Slurry
The first-class industrial alumina with a purity of 99% is added with about 5% of additives to prepare 95% porcelain material, and ball milling is carried out according to the ratio of material: ball: water = 1: 2: 1, and binder, deflocculant and appropriate amount of water are added to prepare stable suspension slurry.The relative viscosity is measured with a simple flowmeter to determine the appropriate mud solid content, type and dosage of deflocculant.
2.1.2 Spray drying process
The main control process parameters in the spray drying process are: a). The outlet temperature of the dryer.Generally controlled at 110℃.b). Inner diameter of the nozzle.Use 0.16mm or 0. 8mm orifice plate. c), Cyclone separator pressure difference, control at 220Pa.
2.1.3 Performance Inspection of Powder after Spray Drying
Moisture determination shall be conducted according to common ceramic moisture determination methods.The particle morphology and particle size were observed by microscope.The fluidity and bulk density of powder are tested according to ASTM experimental standards for fluidity and bulk density of metal powder. The method is: under the condition of no vibration, 50g powder (accurate to 0. 01g) passes through a glass funnel neck with a diameter of 6mm and a length of 3mm for its fluidity;Under the condition of no vibration, the powder passes through the same glass funnel and falls into a container 25mm high from the same glass funnel. The non-vibrating density is the loose packing density.
3.1.1 Preparation of slurry
Using spray drying granulation process, the preparation of slurry is a crucial key. Solid content, fineness and fluidity of mud will directly affect the output and particle size of dry powder.
Because the powder of this kind of alumina porcelain is barren, it is necessary to add a proper amount of binder to improve the forming performance of the blank.Commonly used organic substances such as dextrin, polyvinyl alcohol, carboxymethylcellulose, polystyrene, etc.Polyvinyl alcohol (PVA), a water-soluble binder, was selected in this experiment.It is more sensitive to environmental humidity, with the change of ambient humidity will significantly affect the properties of dry powder.
Polyvinyl alcohol has many different kinds, different degrees of hydrolysis and degree of polymerization, which will affect the spray drying process. Its general hydrolysis degree and polymerization degree will affect the spray drying process. Its dosage is usually 014 - 015wt%.The addition of too much will cause the spray granulation powder to form hard dry powder particles to prevent particles from deforming during pressing.If the particle characteristics can not be eliminated during pressing, these defects will be stored in the green body and can not be eliminated after firing, which will affect the quality of the final product. Binder addition too little green strength will increase the operation loss. The experiment shows that when a proper amount of binder is added, the section of green billet is observed under the microscope. It can be seen that when the pressure is increased from 3Mpa to 6Mpa, the section is increased smoothly, and there are a small number of spherical particles. When the pressure is 9Mpa, the section is smooth, and there are basically no spherical particles, but the high pressure will lead to the stratification of green billet.PVA is opened at about 200 ℃
Start to burn, and drain at about 360 ℃.In order to dissolve the organic binder and wet the billet particles, form the liquid interlayer between the particles, improve the plasticity of the billet, reduce the friction between the particles and the friction between the materials and the mold, promote the density increase of the pressed billet and the homogenization of the pressure distribution, and also add the appropriate amount of plasticizer, commonly used are glycerin, ethyl oxalic acid, etc.
Because the binder is an organic macromolecular polymer, the method of adding the binder into the slurry is also very important.It is the best to add the prepared binder into the uniform mud with the required solid content.In this way, the undissolved and undispersed organic matters can be avoided to be brought into the slurry, and the possible defects after firing can be reduced.When the binder is added, the slurry is easily generated by ball milling or stirring. The air wrapped into the droplet is in the dry powder, which makes the dry particles hollow and reduces the volume density. In order to solve this problem, defoamers can be added.
Due to economic and technical requirements, high solid content is required.As the production capacity of the dryer refers to the evaporation water per hour, the slurry with high solid content will significantly increase the dry powder output. When the solid content increases from 50% to 75%, the output of the dryer will increase by two times.
Low solid content is the main reason for the formation of hollow particles.In the process of drying, water migrates to the surface of the droplet and carries solid particles, which makes the inner part of the droplet hollow; if a low permeability elastic film is formed around the droplet, due to the low evaporation speed, the temperature of the droplet increases, and the water evaporates from the inner part, which makes the droplet bulge.In both cases, the ball shape of particles will be destroyed, and hollow annular or apple shaped or pear shaped particles will be produced, which will reduce the fluidity and bulk density of dry powder.In addition, slurry with high solid content can reduce
In short drying process, the reduction of drying process can reduce the amount of adhesive transferred to the particle surface along with the water, so as to avoid that the binder concentration on the particle surface is greater than the center, so that the particles have a hard surface, and the particles do not deform and crush in the process of pressing and forming, so as to reduce the body mass of the billet. Therefore, in order to obtain high-quality dry powder, the solid content of the slurry must be increased.
The slurry used for spray drying should have enough fluidity and as little moisture as possible.If the viscosity of slurry is reduced by introducing more water, not only the energy consumption of drying is increased, but also the bulk density of product is reduced.Therefore, it is necessary to reduce the viscosity of slurry with the aid of coagulant.The dried slurry is composed of several microns or smaller particles, which can be regarded as a colloidal dispersion system.The theory of colloidal stability shows that there are two forces acting on the suspension particles: van der Waals force (Coulomb force) and electrostatic repulsion force. If the force is mainly gravity, agglomeration and flocculation will occur.The total potential energy (VT) of the interaction between particles is related to their distance, during which VT at some point is the sum of the gravitational energy VA and the repulsive energy VR.When VT between particles presents the maximum positive potential energy, it is the system of depolymerization.For a given suspension VA is certain, so the stability of the system is those functions that control VR: the surface charge of particles and the thickness of double electric layers.The thickness of the bilayer is inversely proportional to the square root of the valence bond and concentration of the equilibrium ion.Double layer compression can reduce the potential barrier of flocculation, so the valence bond and concentration of equilibrium ions in the solution are required to be low.The commonly used demulsifiers are HCI, HNO3, NaOH, (CH) 3noh (quaternary amine), GA, etc.
Because the water-based slurry of 95 alumina ceramic powder is neutral and alkalescent, many coagulants which have good diluting effect on other ceramic slurry lose their function.Therefore, it is very difficult to prepare the slurry with high solid content and good fluidity.The barren alumina slurry, which belongs to amphoteric oxide, has different dissociation processes in acid or alkaline media, and forms the dissociation status of different micelle composition and structure. The pH value of slurry will directly affect the degree of dissociation and adsorption, resulting in the change of ζ potential and the corresponding flocculation or dissociation
Alumina slurry has the maximum value of positive and negative ζ potential in acid or alkaline medium.At this time, the viscosity of the slurry is in the lowest value of the state of de coagulation, while when the slurry is in the neutral condition, its viscosity increases, and flocculation occurs.It is found that the fluidity of the slurry is greatly improved and the viscosity of the slurry is reduced by adding a proper demulsifier, so that its viscosity value is close to that of water. The fluidity of the water measured by a simple viscometer is 3 seconds / 100 ml, and the fluidity of the slurry is 4 seconds / 100 ml. the viscosity of the slurry is reduced, so that the solid content in the slurry can be increased to 60%, and a stable packing can be formed.As the production capacity of the dryer refers to the evaporation of water per hour, so the suspension.
3.1.2 Control of main parameters in spray drying process
The air flow pattern in the drying tower affects the drying time, retention time, residual water and wall sticking of the droplets.In this experiment, the droplet air mixing process is mixed flow, that is, the hot gas enters the drying tower from the top, and the atomizing nozzle is installed at the bottom of the drying tower, forming fountain spray, and droplet is parabola, so the droplet mixing with the air is countercurrent, and when the droplet reaches the top of the stroke, it becomes a downstream flow and spray into conical shape.As soon as the droplet enters the drying tower, it will soon reach the maximum drying speed and enter the constant speed drying stage. The length of the constant speed drying stage depends on the moisture content of the droplet, the viscosity of the mud, the temperature and humidity of the dry air. The boundary point C from the constant speed drying stage to the rapid drying stage is called the critical point. At this time, the surface of the droplet can no longer maintain the saturated state by the migration of water,With the decrease of evaporation rate, the temperature of droplets increases, and the surface of droplets at point D is saturated, forming a layer of hard shell. Evaporation moves to the interior, and the drying rate continues to decline. The further elimination of water is related to the moisture permeability of the hard shell.Therefore, it is necessary to control the reasonable operation parameters.
The moisture content of dry powder is mainly determined by the outlet temperature of spray dryer.The moisture content affects the bulk density and fluidity of dry powder, and determines the quality of pressed blank.PVA is sensitive to humidity. Under different moisture content conditions, the same amount of PVA can cause different hardness of the surface layer of dry powder particles, which makes the determination of pressure fluctuate and the production quality unstable during the pressing process. Therefore, the outlet temperature should be strictly controlled to ensure the moisture content of dry powder. Generally, the outlet temperature should be controlled at 110 ℃, and the inlet temperature should be adjusted accordingly.The inlet temperature is not more than 400 ℃, generally controlled at about 380 ℃.If the inlet temperature is too high, the hot air temperature on the top of the tower will overheat. When the mist drops rise to the highest point and encounter overheated air, for the ceramic powder containing binder, the effect of the binder will be reduced, and finally the pressing performance of the dry powder will be affected.Secondly, if the inlet temperature is too high, the service life of the heater will also be affected, and the heater skin will fall off and enter the drying tower with hot air, polluting the dry powder.Under the condition that the inlet temperature and the outlet temperature are basically determined, the outlet temperature can also be adjusted by the pressure of the feed pump, the pressure difference of the cyclone separator, the solid content of the slurry and other factors.
Pressure difference of cyclone separator.The pressure difference of the cyclone separator is large, which will increase the outlet temperature, increase the collection of fine particles and reduce the yield of the dryer.
3.1.3 Properties of spray dried powder
The fluidity and packing density of alumina ceramic powder prepared by spray drying method are generally better than those prepared by usual process. The powder of manual granulation can not flow through the detecting device without vibration, and the powder of spray granulation can do this completely. Referring to the ASTM standard for testing metal powder fluidity and bulk density,The bulk density and fluidity of particles obtained by spray drying under different water content conditions were measured. See Table 1.
Table 1 loose density and fluidity of spray dried powder
Table 1 Powder density and flow rate
Moisture content (%) |
1.0 |
1.6 |
2.0 |
2.2 |
4.0 |
Density of tightness (g/cm3) |
1.15 |
1.14 |
1.16 |
1.18 |
1.15 |
Liquidity (s) |
5.3 |
4.7 |
4.6 |
4.9 |
4.5 |
The moisture content of spray dried powder is generally controlled at 1 - 3%. At this time, the fluidity of powder is good, which can meet the requirements of pressing molding.
DG1 is the density of hand-made granulation powder, and DG2 is the density of the powder for spray granulation.
The hand granulated powder is prepared by ball milling, drying, sieving and granulation.
Table 2 density of pressed powders formed by manual granulation and spray granulation
Table 2 Green Body’s density
Pressure (MPA) |
4 |
6 |
8 |
10 |
12 |
14 |
DG1 (g/cm3) |
2.32 |
2.32 |
2.32 |
2.33 |
2.36 |
2.4 |
DG2 (g/cm3) |
2.36 |
2.46 |
2.53 |
2.56 |
2.59 |
2.59 |
The particle size and morphology of the powder were observed by microscope.It can be seen that the particles are basically solid spherical, with clear interface and smooth surface. Some particles are apple shaped, pear shaped or bridged, accounting for 3% of the total. The particle size distribution is as follows: the maximum particle size is 200 μ m (< 1%), the minimum particle size is 20 μ m (individual), most particles are about 100 μ m (50%), and most particles are about 50 μ m (20%).The powder produced by spray drying is sintered at 1650 degree and the density is 3170g/cm3.
(1) 95 alumina slurry with 60% solid content can be obtained by using PVA as binder, adding proper coagulant and lubricant.
(2) reasonable control of spray drying operation parameters can get ideal dry powder.
(3) by adopting spray drying process, 95 alumina powder, which is suitable for bulk dry pressing process, can be produced. Its loose density is about 1. 1g/cm3 and the sintering density is 3170g/cm3.
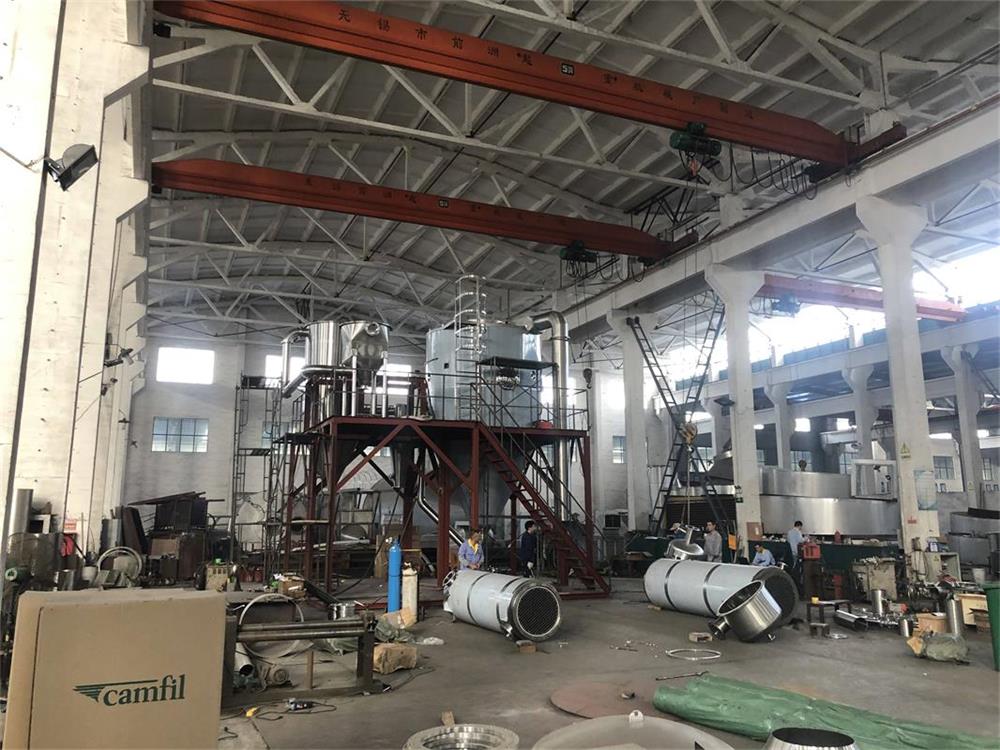
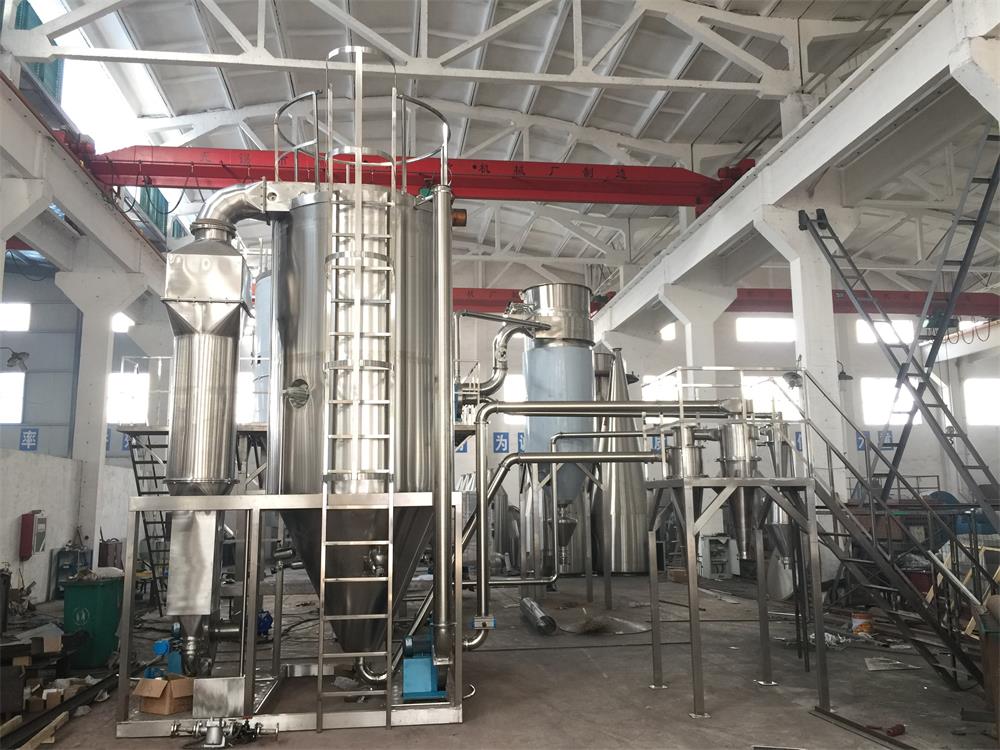